🦾 Top Mistakes to Avoid in Factory Automation
Automation can boost efficiency and improve productivity, but without the right plan, it risks becoming a costly problem.
Automation is transforming industries, particularly in manufacturing, where efficiency, cost savings, and increased productivity are essential. It helps achieve all these goals by streamlining processes, which saves time and money. However, without careful planning and consideration, automation projects can encounter significant obstacles or be abandoned all together, thought to be a waste of time, money, and energy.
Here are key challenges businesses face when implementing automation and how to overcome them.
1. Avoiding the "One-Tool-Fits-All" trap
Many companies make the mistake of relying on a single automation tool, like Robotic Process Automation (RPA), to solve all their challenges. While these tools can be beneficial, using only one solution limits flexibility, growth, and the potential for improvement in ways that may not have been thought by another system.
The key to avoiding this pitfall is starting with the business outcomes in mind and selecting a variety of technologies that work together to achieve those goals. Indeed, every industry or business has unique processes. Automation solutions must be tailored to fit these specific needs, or they might not work as efficiently as expected.
2. Overlooking IT: a risky shortcut
As automation becomes more accessible through low-code and no-code platforms, businesses often think they can bypass IT involvement. However, this can lead to system failures, especially when automation tools interact with existing data systems that require updates and maintenance. IT plays a critical role in ensuring smooth integration and long-term sustainability.
Working closely with IT on the automation project will help ensure the systems are well-maintained and scalable. Automation affects employees and workers alike; involving them early in the process is key to a smooth transition and long-term success. If not handled carefully and transparently, it can lead further down the road to resistance or issues with training and adaptation.
3. Leaving out key players in decision-making
Automation initiatives often affect multiple departments, from operations to HR to security. Failing to involve all relevant stakeholders can create blockages and resistance during implementation.
For example, if automation is bound to change employees’ roles, HR must be involved to manage the transition. Similarly, IT and security need to assess potential risks, such as data access and system requirements.
Ensuring that all voices are heard from the beginning will result in smoother adoption and alignment within all the impacted sectors.
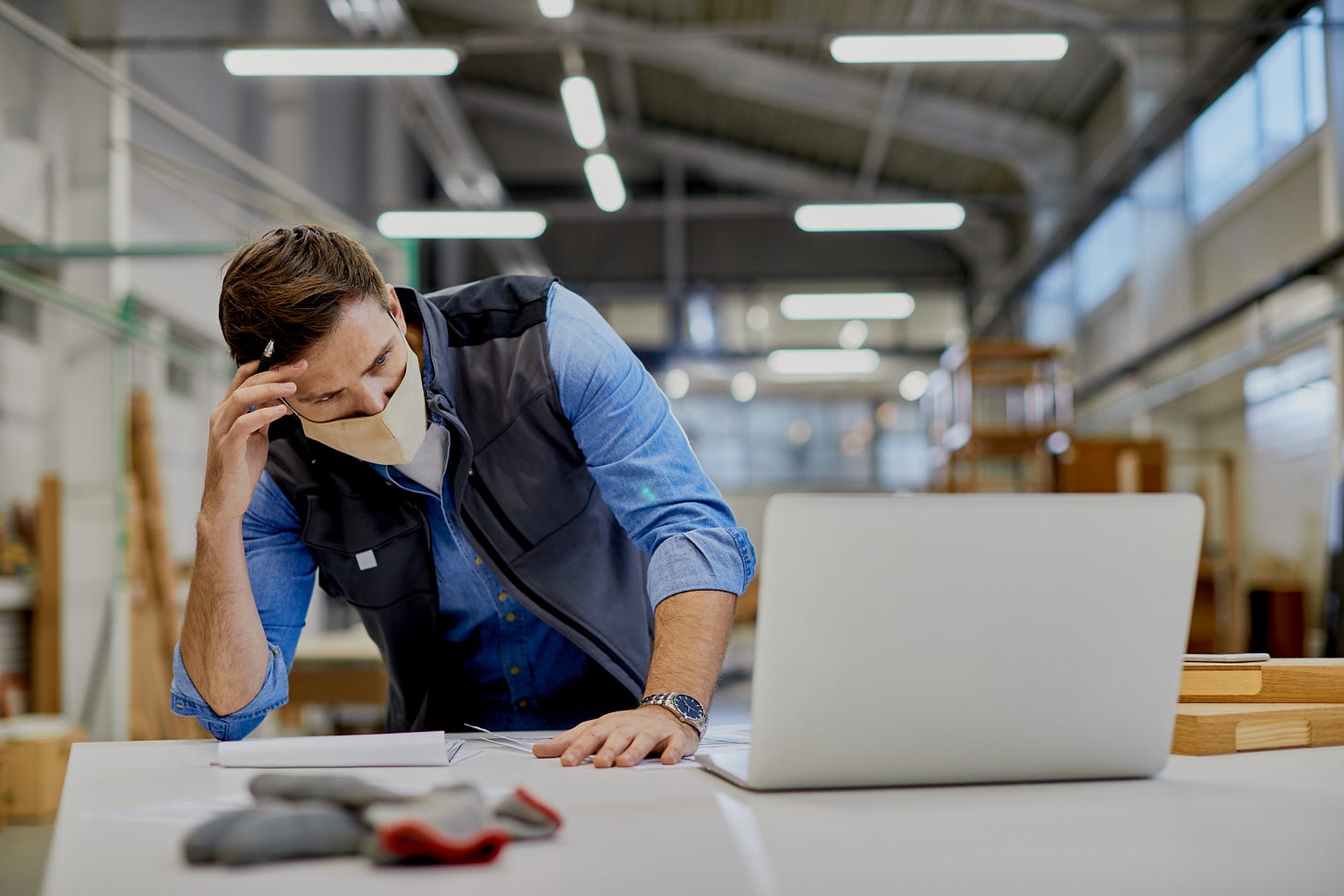
4. Skipping thorough testing: a costly mistake
Automation tools are only as effective as their configuration. If systems aren’t thoroughly tested, they can cause data errors, inefficiencies, or fail to deliver the desired outcomes. Even seemingly simple automation technologies need rigorous testing to ensure they work across the entire business process. This includes not only testing the tool itself but also assessing its impact on workflows and data integrity.
Taking the time to properly test automation systems prevents errors and ensures reliability and usage.
5. Neglecting post-launch monitoring
Many companies assume that once automation is implemented, the work is done. In reality, ongoing monitoring and maintenance are essential to keep systems functioning at their best. Without regular post-launch evaluations, automation systems can degrade over time, leading to inefficiencies and data issues.
Establishing protocols for continuous monitoring ensures that automation continues to deliver value and meet business objectives over the long term.
For example, after automating their manufacturing processes, Siemens implemented continuous monitoring through its MindSphere platform, a cloud-based system that collects and analyzes production data in real time. This allows Siemens to track machine performance, detect anomalies early, and predict maintenance needs before issues occur.
Conclusion
Automation can greatly improve industries, but it comes with challenges. Each step, from choosing the right tools to ongoing monitoring, needs careful planning and collaboration, as we saw earlier in the article.
To give an example, Ford's success with automation, especially through real-time data analysis, helps them detect issues early, cut costs, and reduce waste.
On the other hand, Boeing's automation in the 787 Dreamliner production faced problems. Robots failed to handle complex tasks, leading to delays and extra costs, showing how poor integration can cause issues.
Automation isn’t a "set it and forget it" solution. Companies that plan, collaborate, and stay proactive are more likely to see long-term success.
More on the subject:
A Beginner's Guide to Assembly Line Automation - Assembly line automation's goal is to boost all aspects of the line to produce goods in a more productive manner. How has it evolved? Let's take a walk.
What are integration costs? - Integration costs are a significant part of robotic automation, encompassing expenses for customizing robots to specific tasks.